HyperMesh汽車排氣系統(tǒng)振動(dòng)有限元分析
2017-01-05 by:CAE仿真在線 來(lái)源:互聯(lián)網(wǎng)
摘要:本文運(yùn)用軟件模塊HyperMesh以及RADIOSS對(duì)某汽車排氣系統(tǒng)進(jìn)行了網(wǎng)格劃分,并進(jìn)行了全系統(tǒng)振動(dòng)分析。分析復(fù)現(xiàn)了試驗(yàn)失效模式,模擬與試驗(yàn)結(jié)果相吻合?;谏鲜瞿P蛯?duì)提高排氣系統(tǒng)耐久特性進(jìn)行了優(yōu)化設(shè)計(jì),成功解決了排氣系統(tǒng)振動(dòng)耐久設(shè)計(jì)問(wèn)題。
1 引言
汽車排氣系統(tǒng)是汽車的重要組成部分,其一端與汽車發(fā)動(dòng)機(jī)相連,其它部件通過(guò)吊鉤、吊耳與汽車底盤相連。汽車排氣系統(tǒng)設(shè)計(jì)需要考慮發(fā)動(dòng)機(jī)振動(dòng)激勵(lì)對(duì)其耐久性的影響,對(duì)于發(fā)動(dòng)機(jī)振動(dòng)激勵(lì)模擬試驗(yàn),實(shí)驗(yàn)室通常都是簡(jiǎn)化為單軸振動(dòng)試驗(yàn)。其實(shí)驗(yàn)規(guī)范為:1)將排氣系統(tǒng)與發(fā)動(dòng)機(jī)連接端固定在振動(dòng)臺(tái)上,在關(guān)鍵部位貼上應(yīng)變片做掃頻分析,找到響應(yīng)最大的頻率點(diǎn);2)在上述頻率點(diǎn)進(jìn)行定頻振動(dòng)試驗(yàn),觀察各焊縫位置在1000萬(wàn)次振動(dòng)下是否會(huì)失效。本文針對(duì)該振動(dòng)試驗(yàn)發(fā)生的耐久失效,運(yùn)用軟件模塊HyperMesh與RADIOSS對(duì)其進(jìn)行了振動(dòng)模擬仿真分析并提供了優(yōu)化設(shè)計(jì),成功解決了失效問(wèn)題。
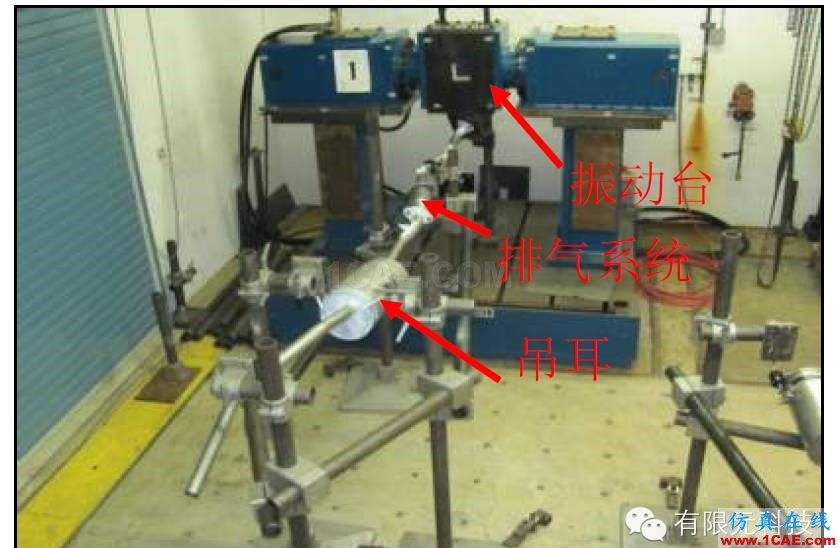
圖1汽車排氣系統(tǒng)振動(dòng)試驗(yàn)圖
圖1所示為汽車排氣系統(tǒng)振動(dòng)試驗(yàn)圖:排氣系統(tǒng)進(jìn)氣法蘭與振動(dòng)臺(tái)連接,其它部件通過(guò)吊鉤吊耳與試驗(yàn)臺(tái)架進(jìn)行連接。
2 試驗(yàn)結(jié)果
按照前述試驗(yàn)方法,先對(duì)排氣系統(tǒng)進(jìn)行了掃頻分析,發(fā)現(xiàn)該系統(tǒng)在120Hz時(shí),各關(guān)鍵部位響應(yīng)最大,固在定頻振動(dòng)試驗(yàn)階段選擇了120Hz作為激勵(lì)頻率;并且在振動(dòng)臺(tái)輸入了垂直方向0.0928mm的位移激勵(lì)。如圖2為試驗(yàn)消聲器進(jìn)氣管失效圖。試驗(yàn)進(jìn)行到180萬(wàn)次振動(dòng)時(shí)消聲器進(jìn)氣管焊縫處發(fā)現(xiàn)裂紋。
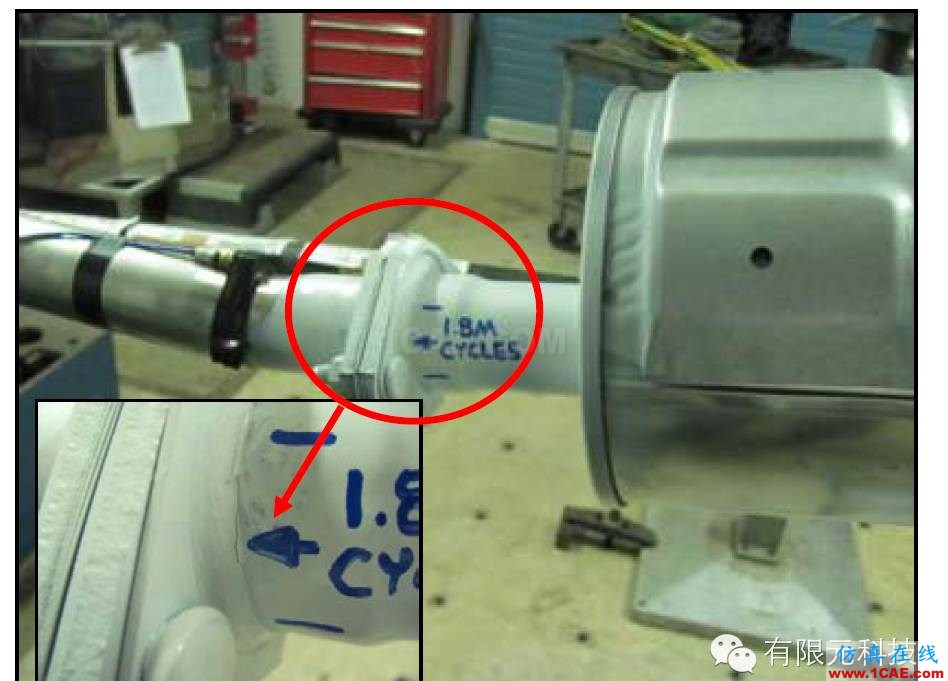
圖2消聲器進(jìn)氣管失效圖
3 有限元分析
為了評(píng)判該設(shè)計(jì)的耐久特性對(duì)其進(jìn)行了有限元分析,如圖3為汽車排氣系統(tǒng)有限元模型,該模型通過(guò)HyperMesh劃分網(wǎng)格并設(shè)置連接方式。模型由兩個(gè)消聲器、五個(gè)吊鉤吊耳以及排氣管等組成。其中消聲器殼體及排氣管用殼體單元模擬,實(shí)芯吊鉤、法蘭用實(shí)體單元模擬,橡膠吊耳用彈性單元模擬。
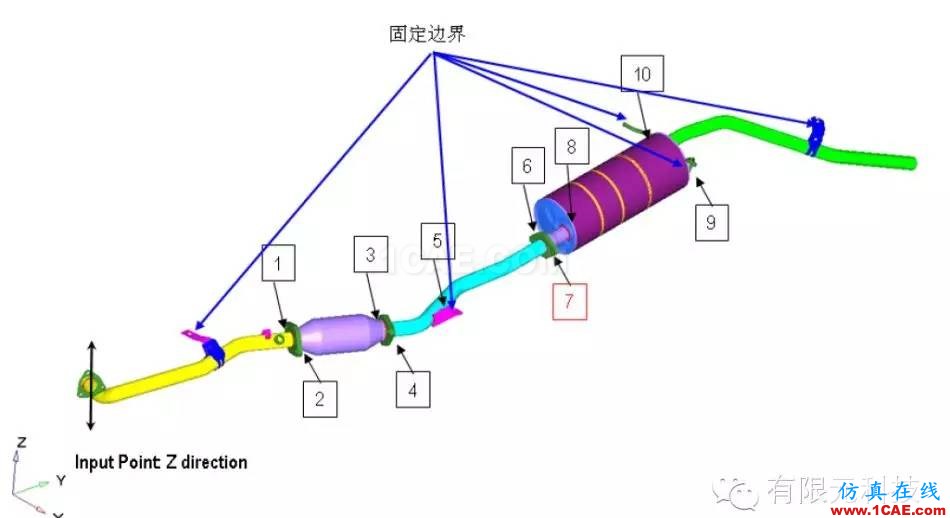
圖3 汽車排氣系統(tǒng)有限元模型
由前述試驗(yàn)知:振動(dòng)失效位置為編號(hào)為7的焊縫處。通過(guò)在HyperMesh中設(shè)置求解,運(yùn)用RADIOSS求解器對(duì)排氣系統(tǒng)進(jìn)行了頻率響應(yīng)分析。分析表明,有限元模型中最大頻率響應(yīng)點(diǎn)發(fā)生在128.9Hz,故在后續(xù)分析中,輸出了排氣系統(tǒng)在128.9Hz時(shí),各焊縫處最大應(yīng)力,計(jì)算結(jié)果如表1。由計(jì)算數(shù)據(jù)可知:編號(hào)為7的焊縫處應(yīng)力最大,與試驗(yàn)失效位置匹配。
表1 排氣系統(tǒng)振動(dòng)激勵(lì)下焊縫處最大應(yīng)力
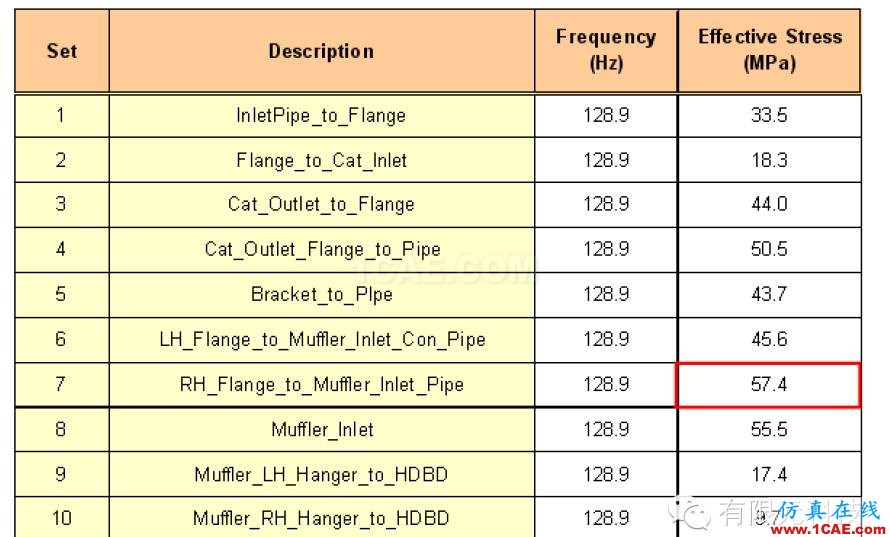
對(duì)比表2與表1編號(hào)為7處的應(yīng)力,可以發(fā)現(xiàn):最大應(yīng)力從57.4Mpa減小到了40.6Mpa,應(yīng)力減小了29.3%,由疲勞壽命公式:N2/N1=(57.4/40.6)5.5=6.6可知,壽命可以提高6.6倍。結(jié)合當(dāng)前的設(shè)計(jì)壽命,其疲勞振動(dòng)次數(shù)可以達(dá)到11.88百萬(wàn)次,滿足設(shè)計(jì)要求。
4 結(jié)論
本文運(yùn)用軟件模塊HyperMesh與RADIOSS成功模擬分析了汽車排氣系統(tǒng)振動(dòng)耐久失效問(wèn)題。結(jié)果表明:模擬方法以及軟件有很高的可靠性,可以為類似問(wèn)題的解決提供參考。
相關(guān)標(biāo)簽搜索:HyperMesh汽車排氣系統(tǒng)振動(dòng)有限元分析 HyperWorks有限元分析培訓(xùn) HyperMesh網(wǎng)格劃分培訓(xùn) hyperMesh視頻教程 HyperWorks學(xué)習(xí)教程 HyperWorks培訓(xùn)教程 HyperWorks資料下載 HyperMesh代做 HyperMesh基礎(chǔ)知識(shí) Fluent、CFX流體分析 HFSS電磁分析 Ansys培訓(xùn) Abaqus培訓(xùn)